design
3-D printing in Fashion
3-D printing is being used to transform manufacturing, medicine, and hobbies, and is also making an appearance in the fashion world. Fashion houses are teaming up with 3-D-printing companies to create signature pieces from 3-D-printed shoes, jewellery, handbags, and clothing.
Design by Noa Raviv
3-D printing is being used to transform manufacturing, medicine, and hobbies, and is also making an appearance in the fashion world. Fashion houses are teaming up with 3-D-printing companies to create signature pieces from 3-D-printed shoes, jewellery, handbags, and clothing.
3-D printing technologies have made an entrance into the fashion industry, particularly haute couture, in recent years, yielding more design innovation. Given the freedom provided by additive manufacturing, it's no surprise that designers are eager to use this technology to create complex shapes and one-of-a-kind pieces.
From shoes to dresses, 3-D printed fashion is vastly different from conventionally manufactured clothing. Each design is unique and personalized and likely the next step toward customization and sustainability, disrupting the traditional the manufacturing model. Another reason why 3-D printing is appealing to this industry is the potential for zero waste and sustainability, a challenge some fashion designers are tackling in their collections.
EXACTLY WHAT IS 3-D printing?
3-D printing, also known as additive manufacturing, is a technique for creating three-dimensional solid objects from digital files. An additive process is used to create a 3-D printed object, which involves laying down successive layers of material to form an object.
What kinds of things can be printed in three dimensions? Car parts, kitchenware, food, toys, prosthetics, scaffolds for human tissue regeneration (to grow replacement body parts such as ears or organs), houses, and, of course, clothing and footwear.
Three-dimensional printing has transformed how we make everything from prosthetic limbs to aircraft parts and even houses.
BENEFITS
Textile refinement, democratization of resources and accessibility, are all potential future developments.
Given the high cost of 3-D printing and the difficulty of producing durable 3-D-printed fabrics that are soft to the touch and drape like traditional fabrics, it is unlikely that it will replace weaving, knitting, and other traditional methods of apparel manufacturing without further development. However, some experts predict that we will be able to print customized garments right in the store, or even from 3-D printers in our own homes one day. Consider having a garment printed to fit exactly to your size and preferences, for example, by using a digital scan of your body with a phone app.You could also experiment with different colors and patterns.To put it another way, it's on-demand digital clothing.
The Fashion Industry's Advantages
"Size wasn't right" and "the garment was damaged" are the top two reasons for online garment returns. The shift to customizable sizes in print-on-demand clothing will result in significant reductions in returns due to size issues or quality defects. 3-D printing is naturally material-efficient because it allows for easy custom sizing. Because the textile of the garment can be created exactly to specifications rather than cut out of a rectangular piece of fabric, resulting in unused remnants, customized 3-D printing of clothing can reduce manufacturing waste.
Recyclability is also a potential benefit of 3-D-printed apparel.
Despite the fact that traditional clothing can be broken down and recycled into new fibers, only about 0.1 percent of textiles collected by charities and take-back programs are recycled. Typically, fabric scraps left over from making a new shirt or dress the traditional way are discarded.
3-D-printed clothing, on the other hand, can be dumped into blender-like machines that turn the plastics into powder that can then be used to print something new.
PROBLEMS
There are numerous benefits, but there are a few drawbacks.
However, many challenges must be overcome before 3-D-printed clothing becomes widely available. The first is the price. Even the most basic home 3-D printers can run into the hundreds of dollars. Individual consumers cannot afford a printer that can print human-sized clothing, and printing a piece of clothing takes far longer than weaving or knitting a similar piece.
Then there is also an issue of comfort. Because it is made of plastic, 3-D-printed fabric is stiffer and less comfortable than traditional fabric. Some designers rectify this with a lightweight fabric lining. Others use FilaFlex, a flexible, rubbery material that is softer and moves and fits the curve of the body.
WHO IS DESIGNING WITH 3-D PRINTING?
Julia Körner
If you've seen the film Black Panther, you've probably already seen one of Austrian architect and designer Julia Körner's most famous designs. She created elaborate structured costumes using 3-D printing in collaboration with with Ruth E. Carter.
Körner made her mark in the fashion industry in 2013 when she collaborated with Iris Van Herpen and the company Materialise to create the first 3-D printed dress.
Her "Chro-Morpho" collection, created in collaboration with Stratasys, aims to show the versatility and diversity of 3-D printing in the fashion world.
Korner has introduced The Sporophyte Collection, which includes three ready-to-wear, high-end fashion pieces. The natural structures found in fungi and kelp inspired Koerner, who is interested in biomimicry.
For the three-piece collection, Körner was able to create beautifully crafted pieces that mimic the movement of wearable fashion garments using this one-of-a-kind combination of flexible rubber-like materials. "It was critical that these intricate pieces kept a flexible aesthetic," Koerner explained. "Designers can use PolyJet digital materials to create flexible pieces that behave more like garments, allowing the material to move with the body."
The Sporophyte Collection was designed by Körner with 3-D printing processes in mind. Traditional manufacturing methods could not create the complex geometric patterns on the jackets and necklace.
"I wanted to incorporate the dried kelp's intricate layering system into the lace-like structure seen in the Kelp jacket and necklace designs." "No other technology can match the complexity, detail, and granularity of this design," Körner added.
Nature is a great source of inspiration, as evidenced by the SETAE jacket, (seen below) which was inspired by a sunset moth in Madagascar.
Over the years, Körner has worked on alternative 3-D printed fashion collections with Iris Van Herpen and Ross Lovegrove. She believes that advances in 3-D printing technology, particularly PolyJet digital materials, have transformed the design possibilities in the fashion industry.
In addition to the introduction of flexible materials, 3-D printing technology has influenced emerging trends in custom-fit clothing. Using 3-D scanners and 3-D printing technology, designers can create tailored pieces for individuals.
"I think it's very exciting to be a part of this group of designers who are looking into how fashion design can be developed using 3-D printing," Koerner adds. My mission is to take this a step further and create customized, ready-to-wear fashion that is appropriate not only for museums but also for the average woman."
Danit Peleg
Much with any new technology, 3-D printing of clothing gravitates toward contemporary design and intricate shapes, all of which are now accessible for home production.
Danit Peleg, an Israeli designer who first used 3-D printing for her graduate collection for a Fashion Design degree, is one of the most vocal supporters of fashion printing.
Danit's products stand out due to their reliance on simple home-use 3-D printers that use the FDM (fused filament fabrication) method, as well as the style of her collections, which bring 3-D printed clothing closer to the pret-a-porte format.
Peleg is the designer of the dress worn by American snowboarder Amy Purdy at the opening ceremony of the 2016 Paralympic Games in Rio de Janeiro, believes 3-D-printed clothing is an unavoidable part of the ongoing digital revolution.
"We used to buy CDs and go to physical stores to get music," she explains, "but now we can just download it from anywhere." "I believe that in the long run, the same thing will happen with fashion — clothes will become more and more digital."
Julia Daviy
Julia Daviy has been working in 3-D printed fashion after becoming enamored with the freedom it allows in terms of material selection and structure. She made the decision to design her own 3-D printed garment, the first "Zero Waste" personalized 3-D printed skirt.
Daviy claims that the skirt generates less than 1% waste during production by using recyclable filaments. This was especially important to her because she sees 3-D printing as ushering in a new era of fashion, allowing a shift away from mass production and toward environmentally friendly manufacturing while utilizing the full potential of available materials. The skirt is made to order according to the customer's specifications.
Ganit Goldstein
For many years, Ganit Goldstein, an Israeli stylist has used 3-D printing to create custom-made clothes that are perfectly tailored to each individual.
"Between the Layers," her first collection, includes seven garments and six pairs of shoes printed in 3-D on Stratasys machines, including a PolyJet that allows for the combination of multiple colors. Goldstein explains that she always starts with a 3-D body scan to tailor her designs to a specific silhouette. She hopes that by doing so, she will be able to provide personalized, comfortable, and tailored clothing for each individual.
Noa Raviv
For her final project, Noa Raviv, a graduate of the Shenkar College of Design in Ramat Gan, Israel, chose to combine traditional 2-D media with the 3-D digital world. Waved garments inspired by distorted digital drawings were made with 3-D-printed elements. To evoke images of corrupted 3-D drawings created with computer modeling software, lines and grids are printed and stitched onto fabrics. She translated those lines into textiles, resulting in an optical illusion.
In black, white, and sheer tones, tulle and silk organza fabrics are layered, ruffled, and pleated into voluminous shapes.
"I chose the materials that I thought had the most innovative look and would fit the best," Raviv explained.
Design by Noa Raviv
Grid-like patterns are warped and stretched across parts of the garments to create optical illusions across the body.
Two 3-D-printed pieces were made from ribbed layers of polymer on a Stratasys Objet Connex multi-material machine. These were sewn onto the shoulder of a backless transparent top and the waist of a calf-length black gown.
The shapes of broken Greek and Roman marble sculptures inspired Raviv's asymmetric silhouettes.
"The silhouettes were influenced by classical sculptures, which served as the collection's inspiration," she explained.
Because those sculptures are rarely found intact, the shapes and patterns in the collection are mostly asymmetrical and appear distorted or fractured."
“The silhouettes were influenced by classical sculptures, which served as the collection’s inspiration.”
In the monochrome collection, orange details are used to edge sections of fabric or chosen as the color for socks.
"In the 3-D software I used, there is a feature that marks the edges of an object with a specific color," Raviv explained. "I used to work in a bright orange color, and this feature aids in error detection." As a result, I felt it was appropriate to include that shade of orange in the collection. White and translucent pieces are edged with black lines, and black material is detailed with white. The plain white and sheer skirts stand out against the exaggeratedly patterned tops.
Iris Van Herpen
Much attention has been given to the work of Dutch designer Iris van Herpen, whose futuristic runway shows were praised by fashion magazines all over the world. In her work, Iris used complex, industrial 3-D printing services, with her designs emphasising the connection between 3-D printing and nature.
She has designed several collections, including "Ludi Naturae," a nature-inspired collection that included the Foliage dress with 3-D printed sheet-like patterns. Iris van Herpen used a PolyJet 3-D printer to create 0.8 mm thick tulle sheets. The designer has also created a number of 3-D printed shoes in collaboration with the United Nude brand.
threeASFOUR
Additive manufacturing contributed to the glowing beauty on the runways at New York Fashion Week. Notably, Stratasys demonstrated its newly developed technique – 3-D printing directly onto fabric as opposed to attaching previously 3-D printed elements to clothing.
Chro-Morpho, a collection inspired by the color morphology and light filtering of insect wings, was created by the AM titan in collaboration with fashion designers threeASFOUR and Travis Fitch. The visual effect of changing shades and depth on a fabric was achieved by 3-D printing fish scale-sized cells made of photopolymers directly onto polyester fabric. The thousands of cells on the 27 parts of the dress are made of a clear lens with colored strips inside.
SHOES
We can see how the benefits of 3-D printing are on display in shoe design. On the one hand we have practical shoes, shoes that are custom fitted to the wearers foot, or designed with maximum foot health in mind. On the other hand we see the full potential of 3D printing in the most outrageously impractical, fantastical shoes that defy traditional shoemaking techniques, designs often inspired by nature, a theme for which 3-D printing seems particularly suited to executing.
3D printing and fashion are merging as designers around the world recognize the technology's potential for creating completely custom clothing and accessories that fit the wearer perfectly.

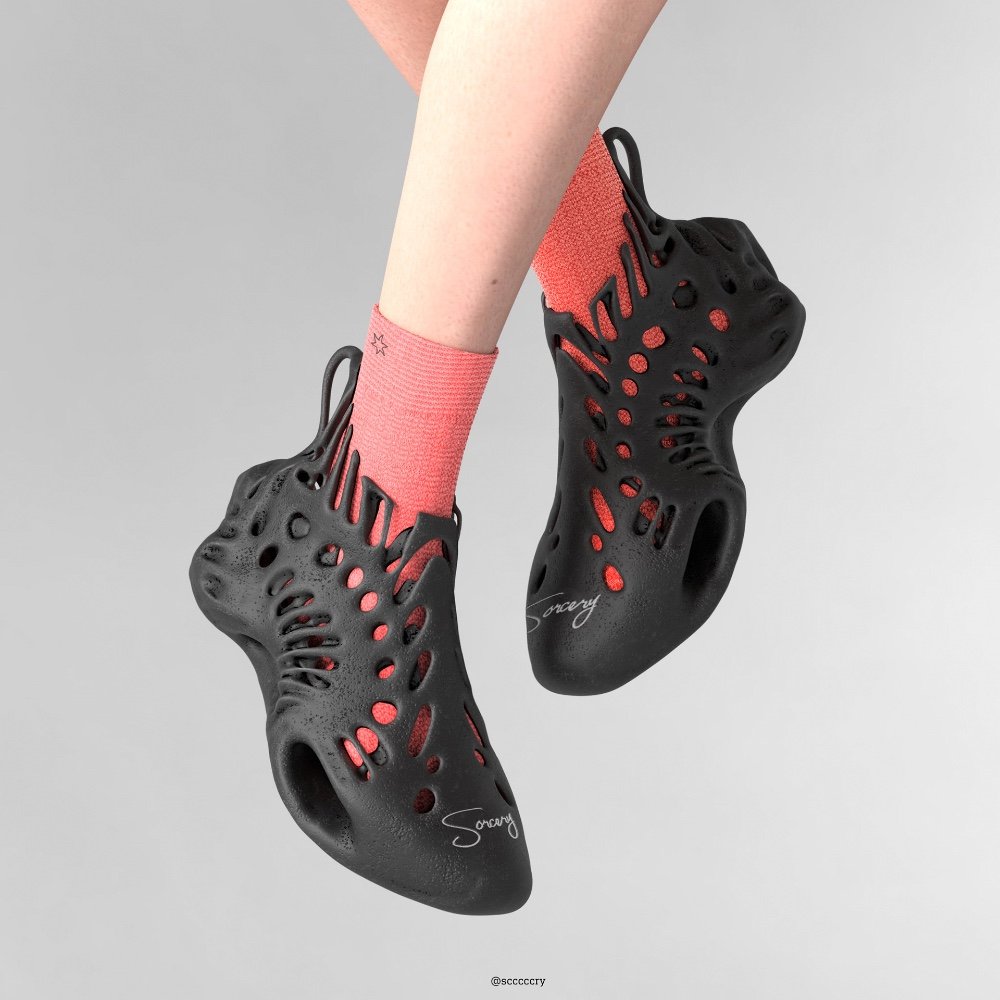


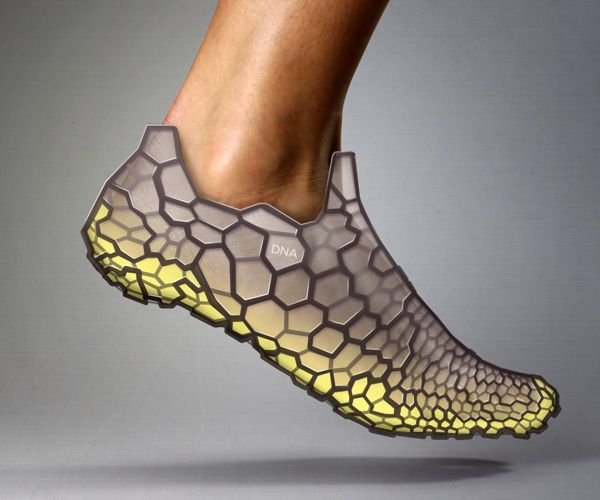

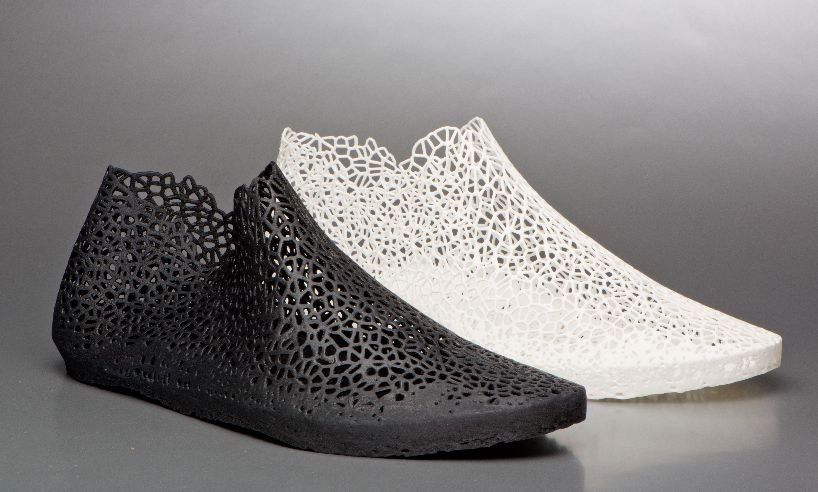
Enjoy the above sampling of more practical 3-D printed shoe designs.
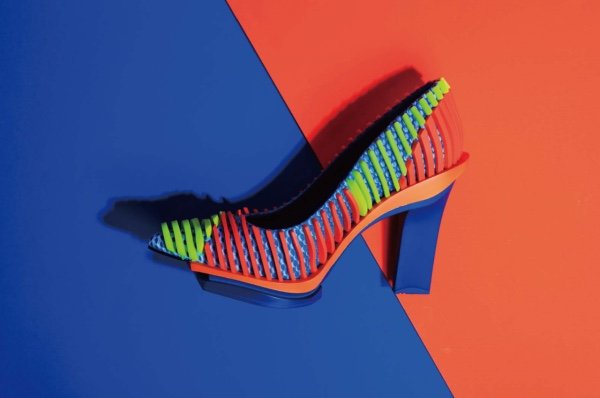
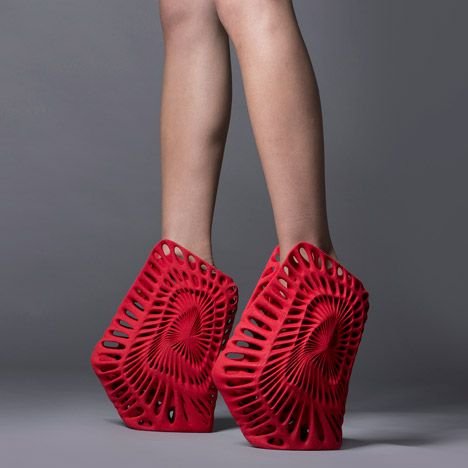
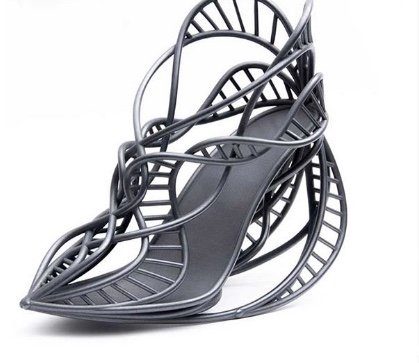
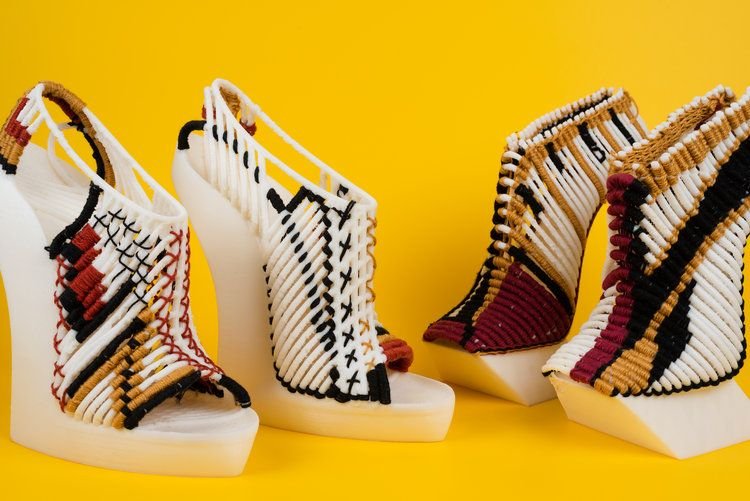
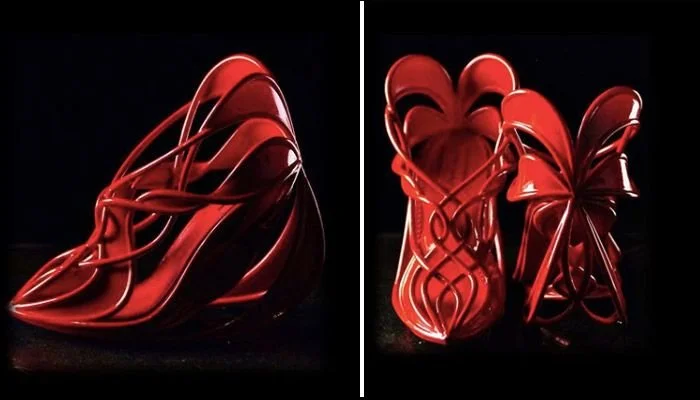
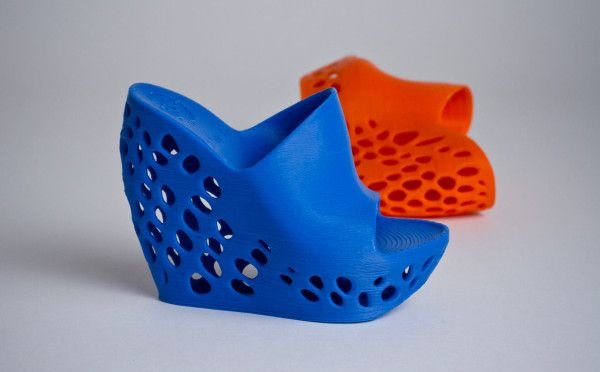
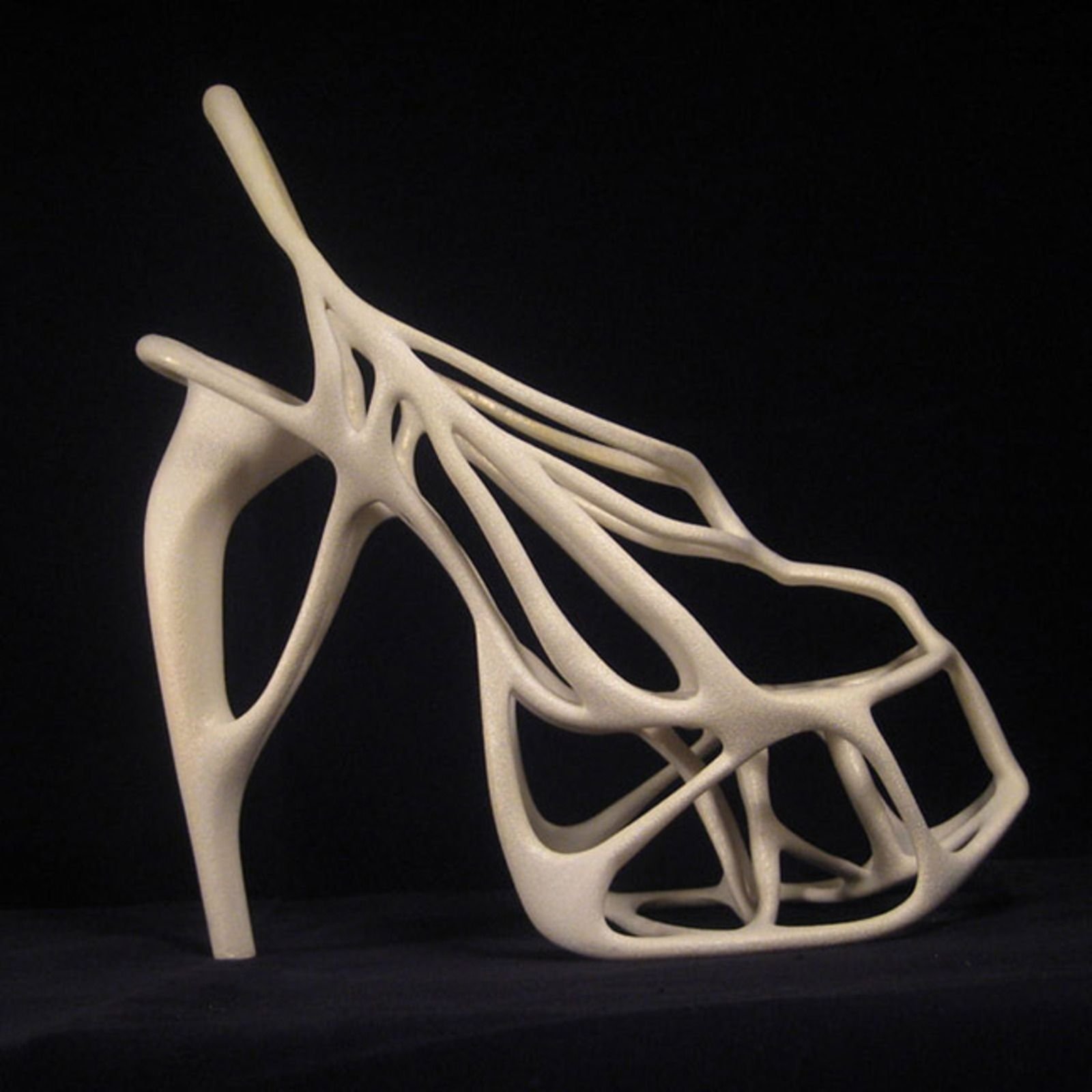
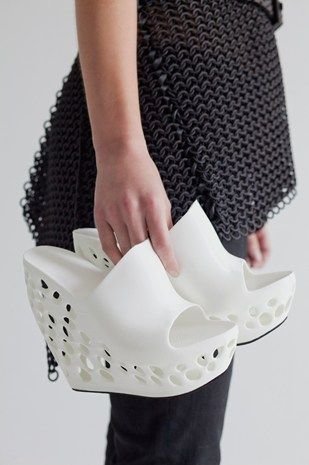
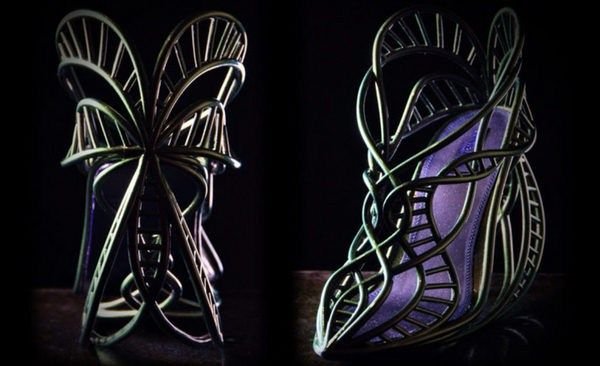
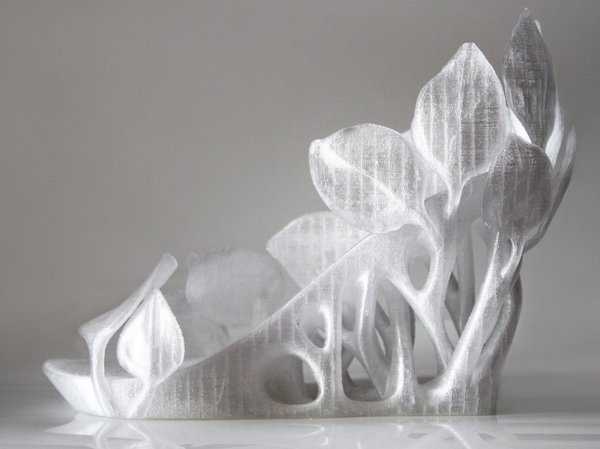
Enjoy the above sampling of less practical and more fantastical 3-D printed shoe designs.
Zoe Dai
Zoe Jia-Yu Dai, for example, has released her "Breaking the 3D Mould" shoe collection. Her designs incorporate traditional shoemaking techniques as well as cutting-edge 3D printing technology.
Dai's initial motivation for creating a partially 3-D printed shoe stemmed from a desire to improve the footwear manufacturing process. It was obvious that 3-D printing could not only accomplish this, but would also give her a great deal of flexibility in the design stage, allowing her to push the boundaries of design structures. She was able to use these ideas while completing her master's degree in footwear design to create the entire shoe collection by combining modern technology (3-D printing) and traditional shoe making techniques.
The process allowed her to push the boundaries of design while also allowing for prototyping, and it created a clear distinction between traditional footwear manufacturing techniques and the techniques she used. She pushed the physical limits of design materials, creating designs that would be impractical, if not impossible, to manufacture using traditional manufacturing methods such as machining or molding.
She was drawn to the idea of combining organic, natural structures with cutting-edge technology. Dai was captivated by the juxtaposition of cutting-edge technology and nature. She also stated that she has always admired the appearance of natural structures and living organisms and wished to incorporate them into her design work. This was especially appropriate for this project because complex structures like these are difficult to produce using traditional machining methods.
Ica and Kostika
Ica & Kostika is a new design studio specializing in the convergence of fashion and technology. The studio emphasizes exclusive made-to-order production while focusing on computational innovation.
KOSTIKA AND ICA The company was founded by footwear designer Ica Paru and architect Kostika Spaho. Ica and Kostika fell in love while working on their 3-D printed shoes in New York City in 2014. The studio is now run by the duo as a fashion footwear brand that pioneers computational design and mass customization.